Comprehensive Guide: What is Porosity in Welding and Exactly How to avoid It
The Science Behind Porosity: A Comprehensive Overview for Welders and Fabricators
Comprehending the detailed systems behind porosity in welding is important for welders and makers pursuing impeccable craftsmanship. As metalworkers look into the midsts of this sensation, they uncover a globe regulated by different aspects that affect the formation of these minuscule voids within welds. From the structure of the base products to the ins and outs of the welding procedure itself, a plethora of variables conspire to either worsen or relieve the existence of porosity. In this thorough overview, we will certainly unravel the science behind porosity, discovering its impacts on weld quality and unveiling progressed methods for its control. Join us on this trip through the microcosm of welding flaws, where accuracy meets understanding in the pursuit of perfect welds.
Recognizing Porosity in Welding
FIRST SENTENCE:
Exam of porosity in welding reveals critical understandings into the stability and quality of the weld joint. Porosity, characterized by the presence of dental caries or gaps within the weld steel, is an usual concern in welding processes. These gaps, if not properly dealt with, can compromise the structural stability and mechanical buildings of the weld, causing possible failings in the finished product.
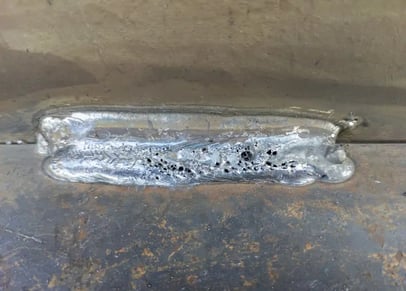
To find and evaluate porosity, non-destructive testing techniques such as ultrasonic screening or X-ray examination are frequently utilized. These strategies enable the identification of interior defects without compromising the integrity of the weld. By examining the size, shape, and distribution of porosity within a weld, welders can make informed choices to enhance their welding processes and attain sounder weld joints.
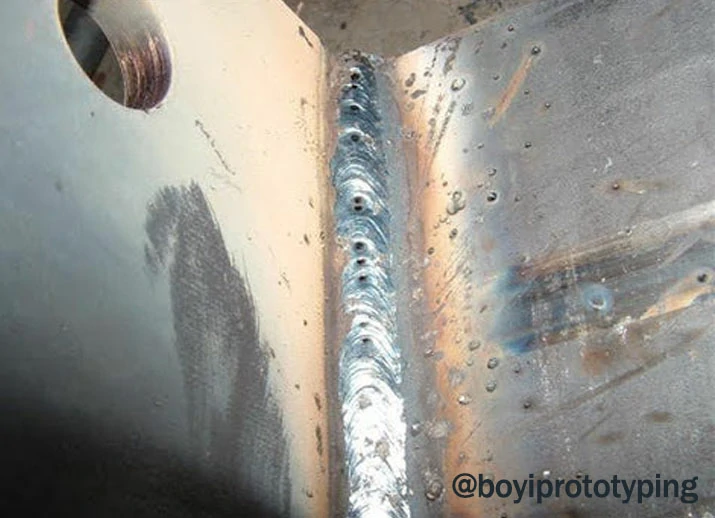
Variables Affecting Porosity Development
The occurrence of porosity in welding is affected by a myriad of factors, varying from gas protecting performance to the ins and outs of welding parameter settings. Welding parameters, including voltage, current, travel speed, and electrode kind, likewise effect porosity formation. The welding method utilized, such as gas steel arc welding (GMAW) or secured metal arc welding (SMAW), can affect porosity development due to variations in warm distribution and gas protection - What is Porosity.
Impacts of Porosity on Weld High Quality
The presence of porosity additionally weakens the weld's resistance to corrosion, as the trapped air or gases within the gaps can respond with the surrounding atmosphere, leading to destruction over time. In addition, porosity can impede the weld's capability to withstand pressure or influence, additional jeopardizing the general top quality and dependability of the welded structure. In essential applications such as aerospace, automotive, or architectural constructions, where safety and security and toughness are critical, the destructive effects of porosity on weld quality can have extreme effects, stressing the value of lessening porosity through next correct welding techniques and treatments.
Techniques to Lessen Porosity
To improve the top quality of welded joints and ensure architectural honesty, welders and makers use particular methods focused on lowering the development of spaces and cavities within the material throughout the welding process. One effective method to minimize porosity is to ensure correct product prep work. This consists of detailed cleaning of the base metal to get rid of any type of pollutants such as oil, grease, or moisture that could add to porosity formation. Furthermore, utilizing the ideal welding parameters, such as the proper voltage, current, and travel rate, is vital in preventing porosity. Keeping a constant arc length and angle throughout welding additionally helps in reducing the possibility of porosity.

Using the proper welding technique, such as back-stepping or using a weaving activity, can also help distribute heat uniformly and minimize the possibilities of porosity development. By implementing these strategies, welders can successfully minimize porosity and generate high-grade bonded joints.
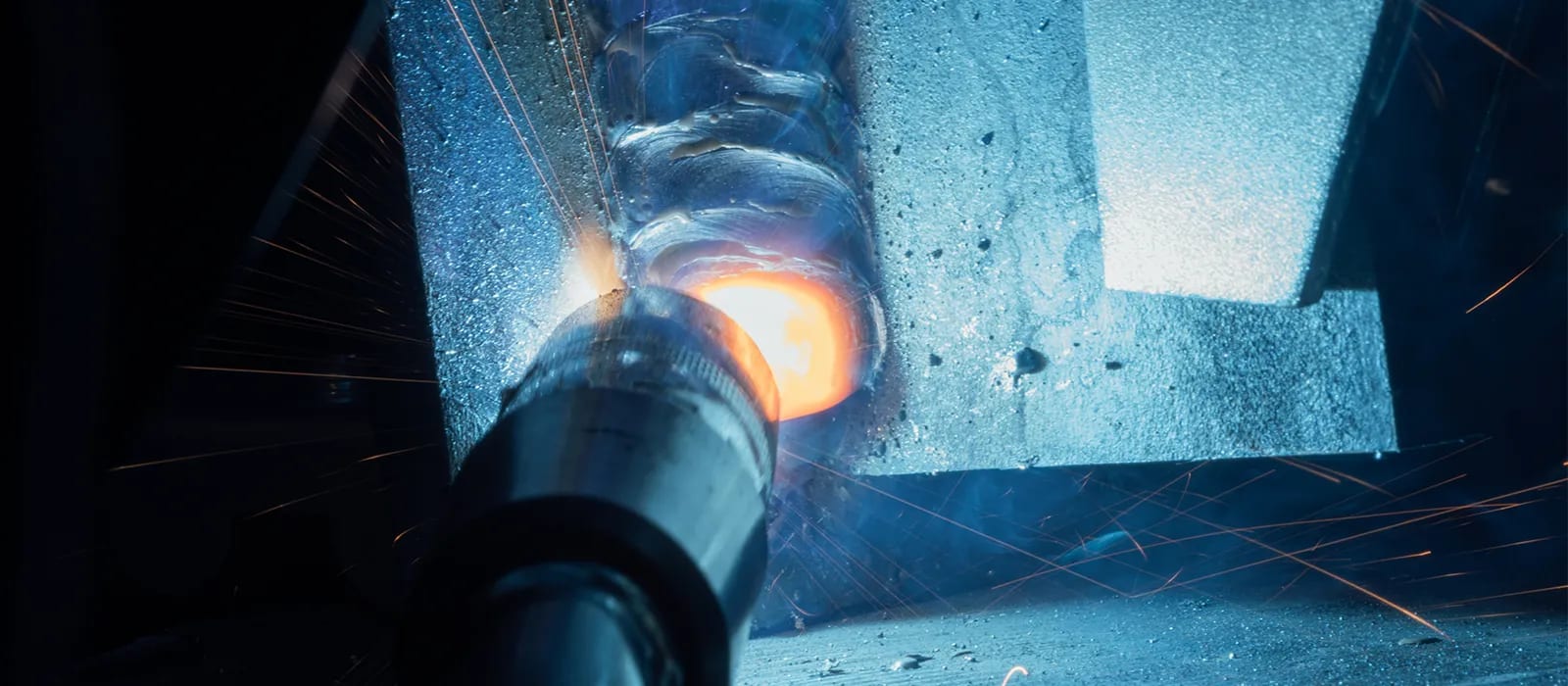
Advanced Solutions for Porosity Control
Carrying out innovative innovations and ingenious approaches plays a critical function in attaining premium control over porosity in welding procedures. One advanced remedy is click over here using innovative gas blends. Shielding gases like helium or a mixture of argon and hydrogen can help in reducing porosity by supplying much better arc stability and enhanced gas insurance coverage. Additionally, utilizing advanced welding techniques such as pulsed MIG welding or customized ambience welding can likewise aid mitigate porosity concerns.
One more innovative option includes making use of advanced navigate to this website welding equipment. Using devices with integrated functions like waveform control and sophisticated power resources can boost weld top quality and reduce porosity dangers. The application of automated welding systems with precise control over specifications can dramatically decrease porosity problems.
Additionally, incorporating innovative monitoring and inspection technologies such as real-time X-ray imaging or automated ultrasonic screening can aid in identifying porosity early in the welding process, enabling immediate restorative activities. In general, incorporating these innovative solutions can substantially improve porosity control and improve the overall quality of bonded components.
Verdict
To conclude, comprehending the science behind porosity in welding is vital for welders and fabricators to produce top quality welds. By recognizing the elements affecting porosity development and implementing strategies to minimize it, welders can improve the total weld quality. Advanced solutions for porosity control can further improve the welding procedure and make sure a solid and trusted weld. It is vital for welders to constantly educate themselves on porosity and apply ideal practices to achieve optimal results.